March 16, 2021 | Company News
Neal Systems is now representing Automation Service for all customers throughout eastern Pennsylvania, Maryland, New York, Delaware, and New Jersey. This addition allows Neal Systems to better serve our industrial customers with the highest quality, shortened lead time and competitively priced remanufactured process control solutions, as well as NEW Foxboro pneumatic instruments.
Automation Service offers a 2-to-3-week standard delivery, a savings of 40-70% on comparable repairs, reliable products, and a 2-year service warranty. The remanufactured products are originally manufactured by Foxboro, Fisher, Rosemount, Honeywell, AMETEK, and Micro Motion. The Foxboro line now includes both new and remanufactured pneumatic transmitters: 43AP, 11DM/GM, 13A, 13FE, and 15A, as well as other pressure transmitters and controllers. There also is a recycling program for your facility where you can receive payment for returns on all of the equipment above.
We know our customers prefer using some products that may no longer be available or have extraordinary repair costs. Automation Service is the perfect solution to keep your tried-and-true products up and running in your plant.
If you have a control valve, actuator, positioner, controller, transducer, regulator, transmitter, magnetic flowmeter, flowtube, vortex flowmeter, or recorders that needs replaced, contact us for a quote for a remanufactured solution!
March 8, 2021 | Product News
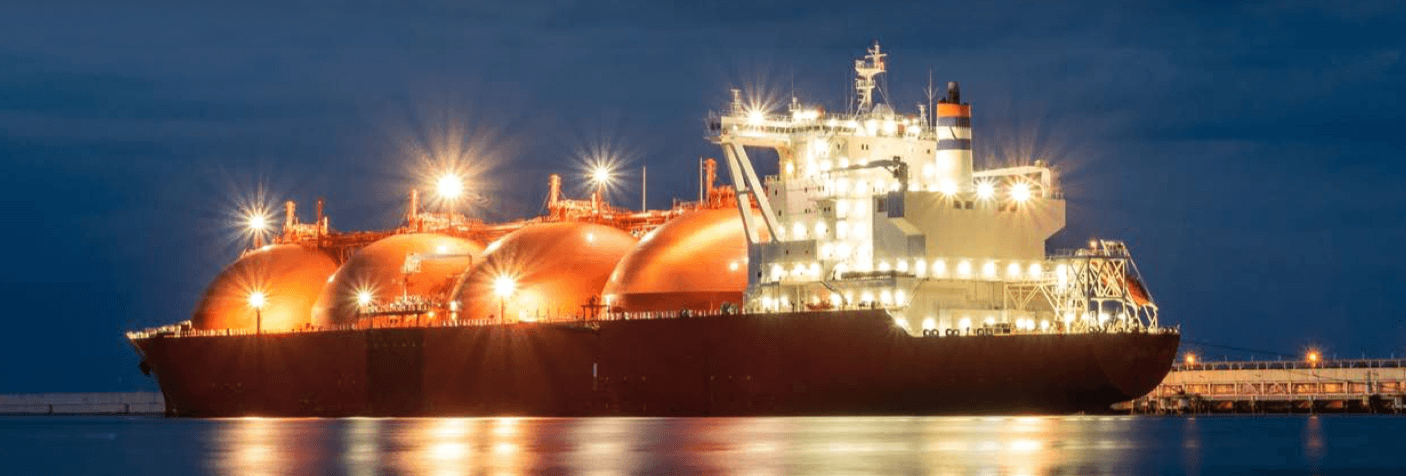
Neal Systems relies on the extensive experience of Servomex when it comes to ensuring the accuracy and reliability for key solutions pertaining to Marine Vapor Control. For more than 30 years Servomex has been providing fixed and portable gas analysis products to marine terminals and tanker vessels involved in the transfer and transportation of crude oil and refined products.
Strict regulations are in place to control the systems used to monitor marine vapors. These govern the performance levels of the analyzer and its suitability to the hazardous environment. Analyzers used in these systems must be approved by the relevant regulatory body.
The vapors produced during loading are either returned to the plant and used for fuel or raw materials, or taken to a safe area and incinerated. In either case, it is essential to monitor the return lines for air ingress, in order to prevent explosive conditions from occurring.
Regulations specify at least two Paramagnetic oxygen analyzers, to ensure redundancy within each system. Our proven solution uses either the SERVOTOUGH Oxy 1900 or SERVOTOUGH OxyExact 2200 analyzers, depending on application conditions. Both offer the enhanced reliability of non-depleting sensor technology, and are approved by regulatory bodies.
SERVOTOUGH Oxy 1900
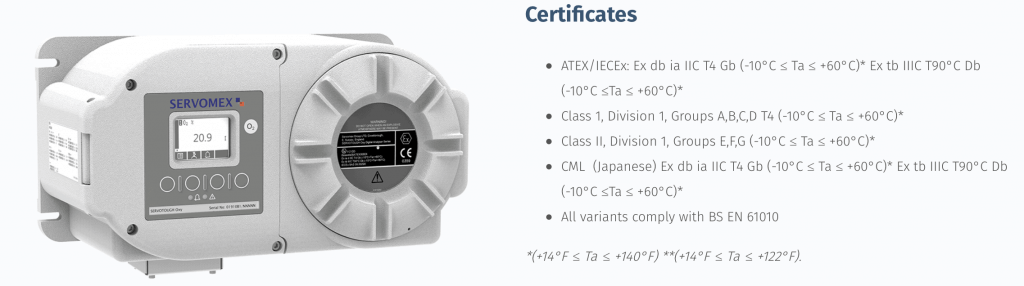
The Oxy 1900 sets the standard for O2 gas analysis, delivering a feature-rich solution designed to meet the monitoring needs of even the most challenging applications.
At the heart of the Oxy 1900 is Servomex’s patent Paramagnetic oxygen sensor, providing highly reliable, accurate and stable percentage measurements of oxygen. The non-depleting technology requires minimal calibration and never needs replacing – ensuring a long lifetime of ownership with low maintenance costs.
The Oxy 1900 combines enhanced-safety design aspects with ease of use and installation, creating an analytical solution that can reduce costs dramatically over product life. It offers clever, value-added features including a heated sample compartment for unrivalled measurement stability and simplified sampling.
SERVOTOUGH OxyExact 2200
OxyExact 2200 Video from Servomex on Vimeo.
The OxyExact 2200 combines high precision Paramagnetic O2 sensing technology into a flexible and robust safety-enhanced design, optimized to meet the needs of demanding process monitoring applications like feedstock purity testing and clean up, hydrogen and chlorine production, solvent recovery and oxidation control processes, ethylene oxide (EO) and ethylene dichloride (EDC) production.
It uses an innovative three-enclosure system that facilitates simplified and versatile sampling of any flammable gas up to 100% O2 (oxygen enriched) – with no need for pre-sample drying – dramatically reducing ongoing costs.
Up to six analyzers can be linked to a single control unit, ensuring the high performance and adaptability required by the most dangerous process control environments.
For more information on the unrivalled performance of the Servomex products, contact one of our expert engineers!
March 4, 2021 | Product News
The AS-410 Vibration Analyzer offers real-time vibration analysis with transient data capture software that can be correlated to external process data like pressures, temperatures, flows, and load. The software merges real-time machinery analyzer, dynamic signal analyzer, transient capture device, modal capture tool, and digital recorder into one powerful package.
The ability of the AS-410 to maintain a large data buffer means the storage of pre-triggered data before an event. This data can be played back and analyzed off-site. The analysis parameters like spectral line and overlap can be changed during playback to avoid potential travel to re-record data.
There are over 50 analysis criteria built-in to the AS-410, which allows it to act as a monitoring system. This allows users to extract different machinery features from the dynamic data. These criteria can be used to trigger data capture and alert the operator.
The user-friendly interface is very intuitive and can quickly open plots, change channels, and modify settings by simply dragging and dropping the different screen elements. The software also allows vibration analysts to quickly navigate and visualize collected data.
The AS-410 has a rich set of available graphical representations of collected data, including time, spectrum, orbits, waterfall (cascade, profile, order), transient/vector (Bode, Nyquist, shaft centerline), transfer functions (magnitude, phase, coherence), trends, scatter, and HMI screen elements (alarm logs, bars, field values, tables, mimics, script buttons).
Finally, the AS-410 has a variety of features that allow the user to quickly annotate and document their analysis. Locking cursors allow the user to correlate and analyze data across multiple pages. Each graphical plot or table can be quickly copied into a word processor or spreadsheet for final report presentation.
For more information on the AS-410, contact one of our expert engineers!