February 17, 2022 | Product News
Monitor various gases and vapours with the modular Dräger REGARD® 3000 control system. Its multi-coloured status light signals the status of your gas detection system. The controller allows you to combine three different modules: Input, Relay and Gateway module. You can connect up to four analogue transmitters and eight relays in combination.
Especially well visible and audible from a distance
In the event of an alarm, every second counts – but it is also useful to be able to see the status of the gas detection system at a glance. The Dräger REGARD 3000 makes this possible with its status light. Different colours clearly indicate whether everything is in order (blue), whether there are malfunctions (yellow) or whether alarms are pending (red). In addition, it can be seen immediately whether the alarm is active (flashing red) or has been acknowledged (continuous red light). This way, everyone on site is informed about the system status and daily checks are also made easier. The integrated horn and the SIL2-capable contacts of the REGARD 3000 provide even more safety.
Access the gas warning system more centrally
Often gas transmitters are installed in areas that are difficult to access or are far away from each other and the associated control unit. The REGARD 3000’s 4 – 20 mA HART® input module gives you central access to all diagnostic information in the event of an alarm or fault. The transmitter configurations can also be read out and transferred conveniently in this way. The intuitive touch display gives you an overview of the status of your gas detection system at all times.
Flexible options for expansion
If the range of functions or the size of the gas detection system changes: The REGARD 3000 can be expanded by an additional relay or gateway module, depending on the requirements. This way, the system remains flexible and grows with the plant without having to shut down the production process for a longer period of time. A REGARD 3000 can be equipped with a maximum of one input module, one relay module and one gateway module.
Networking individual systems with each other
Do you have several gas detection systems with REGARD 3000 and REGARD 7000? You would like to have all systems in view and control and configure them centrally? Then connect the REGARD 7000 as client to the REGARD 3000 systems via an Ethernet cable connection. Networked in this way, the client can detect, control and configure the REGARD 3000 units as satellites.
Flexible options for mounting
You already have a control cabinet or control station for your production process control system and would like to integrate the gas warning system there? Or you need a small gas detection system that can be easily integrated into your building? With the Dräger REGARD 3000, you have the option of integrating the docking station directly into a control cabinet and mounting the operating unit (display module) in the control cabinet door. Or you can use the smart, compact wall-mounted housing. You can choose between the colours telegrey and black.
For more information on the REGARD 3000 contact us here!
February 14, 2022 | Product News
Are unplanned downtime and high maintenance costs hindering your productivity goals?
Relying on Automation Service to fulfill your process control requirements lets you focus on what matters in today’s competitive energy market: enhancing efficiency, lowering emissions, improving your facilities.
Keeping a laser-focus on these production goals while sticking to your budget is easy when you partner with Automation Service. With account executives, engineers, and technicians all working together on your unique project, you can rest assured you’ll receive the highest-quality instrumentation that’s tailor-made for your timeframe, budget, and application.
And when you have Automation Service to count on, unplanned downtime doesn’t have to be stressful. Our expedited shipping process allows custom orders to be on the way in a little as two days, letting you get back to normal operations in a flash.
February 10, 2022 | Company News
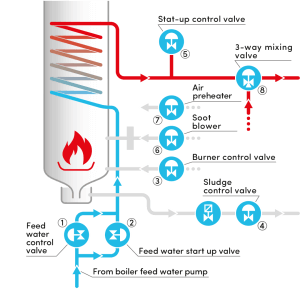
With ARCA Valves you will find the right control valve for each process step in the boiler of the power plant.
1) Main/feed water control valve
With this control valve, the level in the boiler drum is regulated so that boiler feed water is continuously available in the boiler for steam generation. In order to compensate for the difference between the characteristic curve of the feed water pump and the operating characteristic of the boiler system, the characteristic curve of the feed water control valve must be designed accordingly.
2)Filling/feed water control valve
The boiler drum is filled by this control valve when the system is started up. Since a large differential pressure and cavitation have to be mastered during start-up, this valve is subject to high stress and thus wear. Therefore, this often small valve is equipped with a hard multi-stage trim and is located in parallel with the main feed water control valve, which must then be designed for maintaining the level.
3) Burner control valve on the boiler
This valve regulates the supply of natural gas to the gas burner or the heating oil to the oil burner on the boiler. During gas operation, the valve regulates to maintain the defined control characteristic and reduce noise. When heating oil is used, this valve functions as an overflow facility and holds the pressure upstream of the oil burner nozzle constant.
4) Sludge control valve
This valve quickly opens for a brief moment to drain a small quantity of boiler feed water for desludging the boiler water drum. Hard internal parts are required to withstand the high differential pressure, cavitation, and abrasion that prevail. The seat faces of this control valve are subject to wear, which is why we recommend installing an additional shut-off valve here.
5) Boiler start-up control valve
The start-up control valve typically blows steam through a silencer system into the atmosphere when the boiler plant is started. Since the steam expands with a high-pressure reduction, this valve usually has an asymmetric design.
6) Soot Blower Control Valve
The walls of the heat exchangers in the boiler are steam-cleaned of soot particles to optimize heat transfer efficiency inside the boiler. To this end, soot blower control valves feed live steam to the soot blower nozzles with minimum actuating time.
7) Air preheater control valve
The burner air is preheated to optimize the effectiveness of the combustion process. The temperature of the burner air is determined by the steam fed to the air preheater via this control valve.
8) 3-way mixing valve
Superheating the steam of the steam turbines while they are running increases plant efficiency and prevents the turbine blades from becoming damaged by condensed drops of liquid. For better energy utilisation of the generated steam, secondary overheating is installed in power plants with higher steam pressures. The heat transferred to the superheater varies greatly due to fluctuating loads and soot deposits in particular. The temperature of the superheater must therefore be regulated. The superheated steam is passed through a pipe coil by means of the 3-way mixing valve, which is located in the water-filled part of the steam drum. The colder drum water with the saturated steam temperature thus cools the superheated steam.
8) Boiler injection cooler
Another way of controlling the superheater temperature is usually implemented in new systems by injecting boiler feed water with a controllable injection cooler.
February 9, 2022 | Product News
Looking for ways to improve your water and wastewater treatment systems?
Working smarter is easy with the right automation instrumentation. Process controls from Automation Service can help you meet your primary water and wastewater treatment plant goals: reduce cost and downtime, stay in compliance and increase operational efficiency.
Whether you’re looking to supplement your plant with a modernized process, retrofit parts of your existing systems, or do a complete overhaul, we can guide you towards the equipment and instrumentation that fits your budget, timeline, and application. You can count on our account executives, engineers, and technicians to give your unique project the attention it deserves.
February 7, 2022 | Company News
Make the Switch!
Don’t get left behind and become susceptible to lost communications with legacy phone line alarm dialers. Below are the top 3 reasons to switch to a wireless, cloud-based monitoring and control solution for your water and wastewater applications.
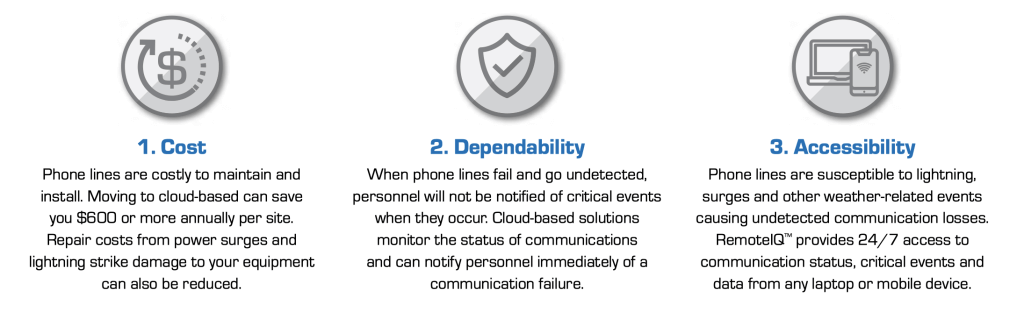
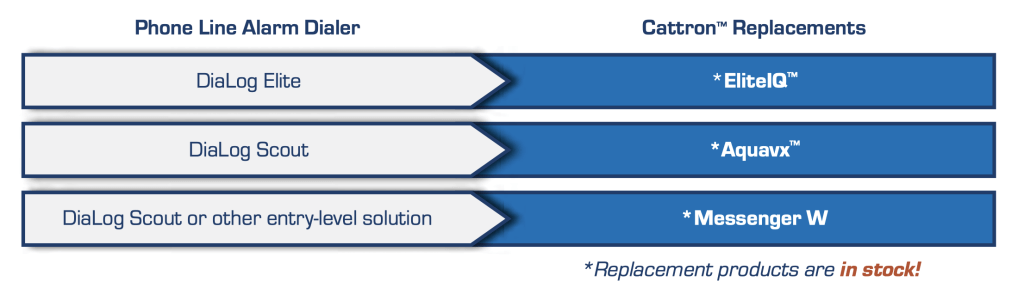